February 2021
How Are We Keeping Busy in the Off-Season?
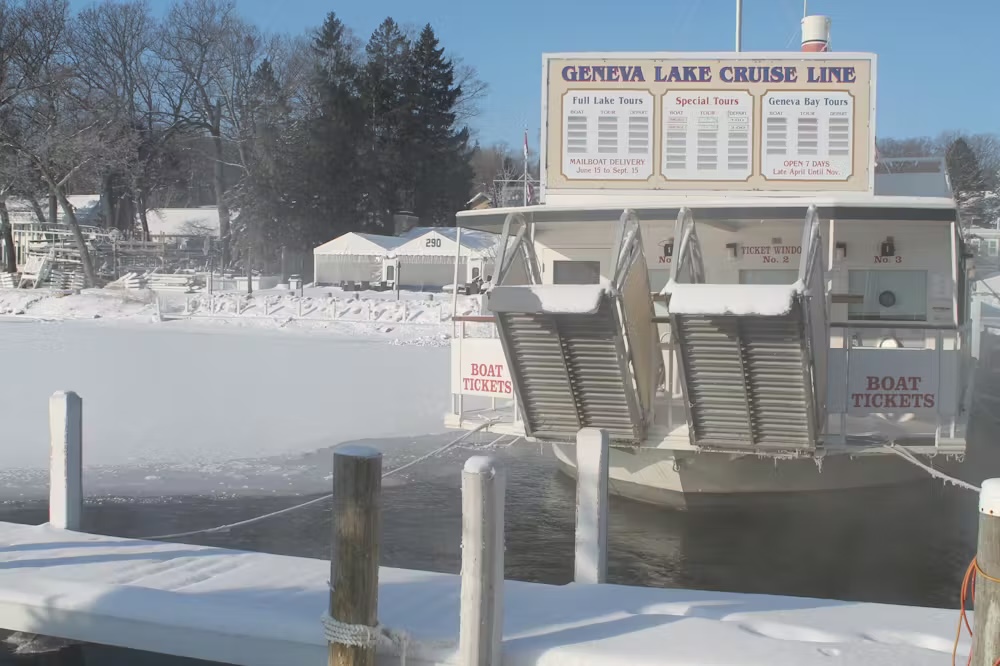
When you work in a seasonal business most people assume that you are off of work during the “off season.” It’s very common to be asked, “What do you do in the off season?” It’s a logical question – boat tours and charters are not running this time of year, so what is there to do? A normal response is, “We get everything ready for the following season!” Of course the pace is slower and the immediate demands are less as compared to “in season” but there are always things to do to keep us busy and to make sure we are ready to open next season. In the off season it takes planning for the future, creative marketing, brainstorming and even lots of physical labor to get properly prepared for the next season.
Here’s the perspective of that off season work from three of our full time employees. Ellen Burling is the Assistant General Manager; Clare Mulcahy is Charter Sales Manager and Jack Lothian is General Manager. Each provides some insight into their role in the off season and what fills their days when the lake is freezing over!
Ellen Burling
When customers take a tour with Lake Geneva Cruise Line, it’s easy! We have a great website that provides detailed information about all of our tours. From that same site a boat tour reservation can be booked. When they arrive for their tour they are met by a trained office staff member who prints their tickets and sends them in the right direction to get on the boat tour they have selected. Once on the tour, more well trained staff are there to assist them and provide them with great service, an interesting narrated tour and a safe environment aboard the boat. If they have chosen to take a meal tour, the menu has been thoughtfully prepared and the service staff has been trained to provide the best experience possible. All of this is smooth and easy for our customers because our full time year ‘round staff works behind the scenes in the off season to make sure it all happens this way. The website and reservation system work smoothly because we work with programmers to make sure it’s all set up correctly. Our staff is well trained because we plan and implement extensive employee training during the off season. Tour rates, meal tour menus, new brochures and other media, the tour narration, and every other aspect of our business are taken into consideration during the off season and changes and updates are made when necessary. These are all things that I work with in the off season.
I used to say that it was a great arrangement to have six months of the year when we were “crazy” busy every day, and six months where we actually had time to think and plan for the next year. That six month timeline changed a bit when we started to offer Santa Cruises a few years ago and were open for tours two more months of the year, but we still have to be cognizant of the planning and preparation that goes into the next season. As soon as the regular season ends we are focused on preparing for Santa Cruises (in a normal non-Covid season) but we are also starting to plan pricing, schedules, menus, etc. for the next season. We take time to evaluate the season that has just ended and talk about potential changes for the next year. Once those decisions are made, lots of updates can begin – our website, tour brochure, social media sites – anywhere that our information is available to the public has to be updated. Our reservation system which is managed by FareHarbor, has to be entirely updated for the next season with new schedules, rates, menus and all other details so that when we make it “live” to the public all details are accurate and correct. The same goes for all printed materials like our tour brochure – lots of double and triple checking goes into these processes.
Another area that takes some time is staffing. We typically have very little turn over from year to year since once people are hired they tend to stay for quite a while, but for those that do move on from this job we have to replace them and/or in general evaluate our staffing needs and hire accordingly. We typically get more applications submitted than we can hire, but we interview anyone who applies and if they seem like a good fit and we have an open spot we will take them on. Our seasonal staff consists of close to 100 people from ages 14-70+ all playing a role to make the cruise line run smoothly. Whether it’s a ticket seller, dock hand, tour guide/boat crew, wait staff, bartender or boat captain (and some do more than one job) everyone works together. Training typically starts right at the beginning of the season for new and returning staff.
The last area that you may not realize we are always working all year ‘round on is sales. Doing advertising and marketing to promote new business is something that we are always doing but it really ramps up in the off season. Much of our group tour business and our private charter business is booked in the off season. Planning for these outings and events requires a good amount of lead time so we often book things like this many months in advance. Our sales staff is constantly looking for ways to promote our businesses through print, digital, trade shows, and social media. We attend a variety of trade shows and conferences while inquiries come in and bookings are made all year long. We have many groups and charter customers that come back year after year, but a good percentage of our business is new each season as well. We all know that we have a great product to sell, so that makes the process much easier. A beautiful and historic lake, a well appointed fleet of eight boats and endless options for creating a unique and memorable experience on Lake Geneva make sales pretty easy! Well now I can add writing blogs to the list of things I do – both in season and off season!
Clare Mulcahy
I was able to check Blog off of my things I get to do in the winter last month when writing about wedding planning in this crazy Covid world we are currently living in. What Ellen mentioned above regarding marketing, brochures, pricing, updating websites and evaluating the past season is true for private charters as well. But one main word is missing, Weddings. One word that can consume most of my winter after some basic office work is completed.
The Charter Department, consisting of Angie Jahns, Robyn Bakken and myself, spend much of November and December putting to bed all of the last year’s events, check billing, invoices, inventory and file away the season both literally and figuratively. We may book a private event aboard one of the Santa Cruises as a Holiday Party but nothing compared to “in season” bookings.
So where then does the word wedding fit into all of this? The Charter Department completes our wrap up around mid November just before Thanksgiving. When do most couples get engaged? The holidays. Ever notice how the jewelry ads start popping up come November? And not just any jewelry, engagement rings. Ready to be purchased before popping the question on Christmas day or New Year’s Eve and hopefully hear the word Yes! Now it is New Year’s Day and you can either watch football or, you guessed it, Say Yes to the Dress. Congratulations, your fiancé will now be taking you to several wedding shows during the next three months and she will become obsessed with wedding magazines, theKnot.com and will start lugging around a binder so large you did not think they existed anymore.
It is my job to make sure that her big binder, WeddingWire saves (don’t ask), Google searches and Pinterest Boards are filled with Lake Geneva Cruise Line wedding images and information. It is marketing dialed in to reach those that never thought of coming up from Chicago for a ‘local destination wedding’ or hosting the engagement party where you say “Bon Voyage” to the single life. I will be at all of the wedding shows tending to our Lake Geneva Cruise Line booth then follow-up with those in attendance. The shows really are not that bad, there is cake and champagne!
Toward the end of February I can stop staring at our gallery of wedding pictures to find just the right one and walk away from analyzing the wedding ad data. It is on to rebuilding bar packages, reviewing new menus, lots of data entry and booking corporate parties that you can read about in next month’s blog!
Jack Lothian
‘Enjoying your time off?’ asks a number of people between January and April. Although we don’t have tours regularly scheduled during these months, we are still hard at work getting ready for the next year. The office staff prepares for the upcoming season and gets some projects done that aren’t possible during the busier seasons of the year. Our maintenance team is also working full time improving and repairing the largest assets of the Cruise Line, the iconic boats in our fleet.
Our maintenance team includes captains and bartenders from the regular season as well as other members of the Gage Marine family, including employees of the marina and Pier 290 staff. Ed Zwiebel and John Friestad have been performing maintenance on the boats in the winter months for decades. Jeff Clapp, a former Tech. Ed. teacher, joined the maintenance team seven years ago to utilize those skills. In the past few years, a couple of our younger college graduates, Kyle Foulke and Douglas Clements, came aboard the team. On the mechanical side, Mike Hackbarth has maintained the engines, generators, and other necessary systems on the boats not only during the off-season, but throughout the year.
Their dedication to keeping the fleet in great can be seen throughout the spring, summer, and fall. Each year a select few boats get more extensive work done, while the entire fleet has general maintenance performed. This year, with the decision to cancel Santa Cruise due to safety concerns, we have taken on a bolder plan of maintenance this winter. The boats that we are focusing on are the Walworth, Geneva, Lorelei, and Harold J Friestad (office barge).
The Walworth, built in 1966 and lengthened in the 80s, has been pulled up on the tracks. These are three railroad tracks that run part way up the hill in front of the Pier 290 restaurant at the Gage Marine lakefront. We use up to eight sections of the big cart to pull the larger boats out of the lake with the help of a winch and cable system. This cart is then chained in six locations to secure it in place during the winter.
A large wooden structure was constructed to protect the project from the elements since many of the jobs need to be completed in a warm and dry environment. Trusses were set on top of the Walworth with uprights supporting the outer ends with thin reinforced plastic covering the entire framework. Exterior propane heaters are then utilized to blow warm air into the enclosed space. This temporary boat house has been dubbed “Fort Walworth”.
The Walworth is not getting a face lift, but it will look slightly different in 2021. Some of the changes will be a new ceiling and floor on the upper deck after repairing sections that had some rust damage. There are a few places that needed leaks plugged and sealed to Other changes will be of a more cosmetic nature.
Due to a leak on the upper deck, there was water getting into the ceiling on the lower level. We removed the wooden floor and aluminum spacers that allowed it to float in place. Underneath was an ice and water shield, a tar product that is normally used on roofs. This presented a tough challenge, removing about an eight inch of tar from the steel floor. It took a week, along with a blow torch, heat guns, large and small scrapers, and paint stripper to remove the sticky gooey substance. We also went through numerous rags and a few pairs of shoes.
A four by ten foot section of steel was replaced and welded in place on the upper deck. This will be primed with a high quality, multistep system that protects it from further rust damage. We will paint the deck with a non-skid additive to give extra traction during wet or snowy weather. We are exploring flooring options that can be installed and removed easily for use during the warmer months, then removed each winter to inspect the condition of the steel. Like most projects, final decisions are being made as we move forward. Also on the upper deck. We are reconfiguring the cabinets to provide more space with the handrails for additional seating. These cabinets are important for the storage of life jackets but moving them outside of the railing allow for an extra row of chairs during tours and additional floor space for charters.
The bathrooms are getting a minor makeover, with new flooring, an updated vanity, replaced blinds, and repainted walls. There are also a few walls in the bar area that will be refinished and/or replaced due to water damage. Other minor tasks include touch-up painting on the hull and sides of the boat as well as re-covering the front counter on the lower deck.
In March, we plan to trade out the Walworth with the Harold J Friestad (HJF) on the cart. This past summer we discovered rust damage in the aft most bilge. To get a better assessment of the situation, we will pull it out of the water and needle scale the rusted area. Needle scaling is a procedure using a pneumatic tool that has a couple dozen steel nails that hammer to remove rust from metal. Depending on the thickness of the metal and the extent of the damage, one can punch a hole through the hull. Because of this, we always needle scale a boat while it is out of the lake. If needed, we will replace a section of the hull.
The Geneva was loaded onto its trailer this November and trailed to the Cruiser Shop at our Theater Road location. The 50 foot launch fits inside with just a few feet to spare on every side. The shop had a renovation a few years ago to accommodate the smallest boats in our fleet. The makeover included new wall panels, reconditioned heating system, and brighter LED lighting.
The Geneva’s deck was showing signs of wear and tear with a few areas of delamination and stress. We replaced the entire deck with a new material that will stand up to whatever Mother Nature can throw at it. We sealed each section of the deck with an epoxy glue to form a watertight coverage before lightly sanding and painting the deck. Each section has been bolted to the metal subfloor framework. Caulk was used to fill the gaps between the floor boards to create a seamless floor, with hatch covers to access the bilge.
Next, the hull has been sanded down to the original fiberglass to clear away all of the old paint that has been applied throughout the years. The hull will be prepped, primed, and repainted in the Gage blue. Other tasks performed on the Geneva will be repainting the catwalk as well as the navigation light boxes. Also, the canvas canopy was removed from the awning superstructure and sent out for some minor repairs.
When the Geneva project has been completed, the Cruiser Shop will house the Lorelei. The main outside deck area will have the wood floor removed so we can repair the metal substructure. There are other minor wood refinishing to be completed as well. We will also take the opportunity to repaint the hull and do any other touch up work that needs to be done.
One boat outside of our fleet that is being worked on by our team is the private yacht, Matriark. This magnificent lake yacht from 1899, has beautiful woodwork that will be stripped, sanded, and refinished. The deck will have a few planks replaced due to weathering before it is sanded and refinished.
In the cabin of the Matriark, the bar area will be reconstructed to include two refrigerators, a dump sink, and an ice bin. Also, two cabinets will be built behind the cabin on the fantail for additional coolers and storage. These cabinets will be constructed to match the quality of woodwork on this lake yacht.
Of course, there are also mechanical upgrades and maintenance that needs to be addressed in the off-season. The Lady of the Lake will have both Caterpillar 3208 diesel engines rebuilt for the 2021 season, while the Walworth is upgrading to a larger generator.
We use Caterpillar diesel engines in the Lady (2), Grand Belle (2), Walworth (2), Polaris (1), and Geneva (1). We also keep one Cat engine on the shelf in case of an emergency during the season. We had to use the extra engine this fall when one of the Lady engines overheated. Since we were already planning on switching out both engines this fall, it worked in our favor allowing us to only pull one engine in December.
If you are wondering how we get a large diesel engine out of the boats, here’s the procedure. We remove the large top hatch that is part of the deck floor. Underneath is a steel cover that is also removed to gain access to the top of the engine. A bar/chain is shackled to lifting points on the top of the engine. Of course, all hoses, wires, exhaust, and the propeller shaft have been detached from the engine. Wooden uprights are set on the deck, with an I-beam set on top (near the ceiling) and clamped in place. A I-beam trolley is installed and a motor hoist is hung underneath. The chain from the hoist is attached to the bar/chain and the engine is lifted off of its mounts, brought up to deck level, slid down the I-beam, and lowered onto wood blocks on the deck. All of the I-beam apparatus is removed so that the pier barge can use its crane to reach inside the boat and pick the engine. It is carried near the shore and loaded onto a flatbed truck or trailer to be brought to a service bay for the rebuild.
So as you can understand, ‘Are you enjoying your time off?’ is a bit of a misnomer to the maintenance team at the Lake Geneva Cruise Line. The maintenance team does love their time driving and bartending during the warmer months, but they also are dedicated to the fleet during the snowy season as well.
Need help choosing the right tour for you?
Our tour finder makes it easy to find the tour that fits your interests, group size, and budget.